What is Cost Accounting?
Cost accounting is a method used in business to track, analyse, summarise, and research a company’s expenses related to any process, service, product, or organisation. Hence for every company today, there is a need for cost accounting.
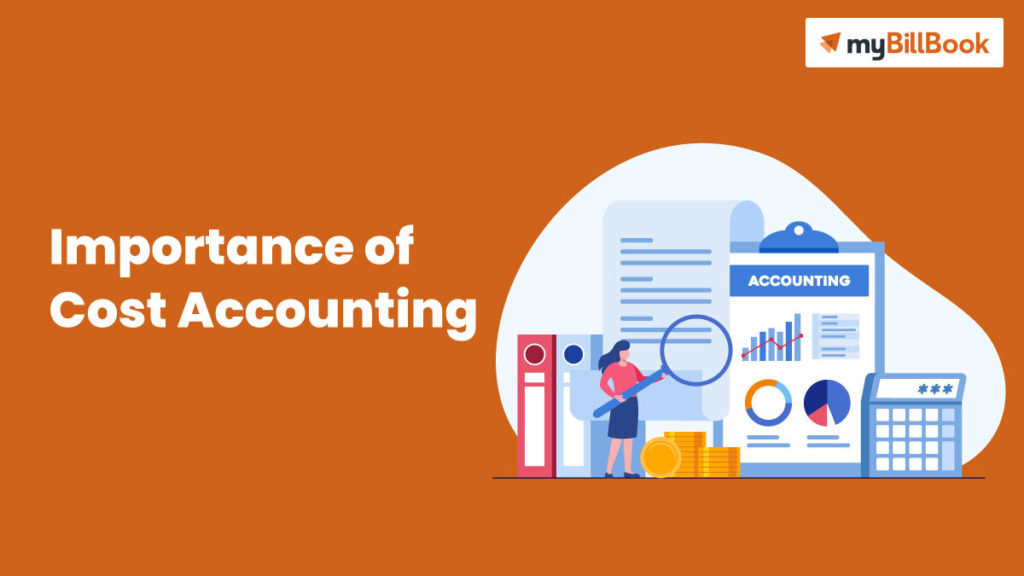
What is the Importance of Cost Accounting?
Cost accounting helps the management in making cost control techniques and strategic planning for your company to increase cost-effectiveness. Additionally, it aids in management’s determination of where they must control the cost. Apart from the needs of cost accounting mentioned, it has many other advantages that can help your business, like:
Managing the Cost of the Product
Your management can predict a product or service’s cost and selling price using cost accounting, enabling you to create business policies. Your management can also come up with ways to keep costs under control while still achieving maximum profitability.
Calculating the Overall Cost Per Unit
Cost accounting procedures establish the overall cost per unit of a good or service and set a selling price for the company.
Displaying Activities Based on Profit
Your management can use this knowledge to stop non-profitable activities while growing and increasing profits.
Cost Comparisons Through Time
You can use data from cost sheets created for multiple periods to compare costs over time for the same good or service.
Cost Accounting Elements
Materials, labour, and costs comprise the three basic cost element categories. Overhead costs are those associated with indirect materials, labour, and expenses.
Material Cost
The price of the raw materials needed to make an item is known as the “material cost. You can classify it as:
- Direct material: is used directly in producing a product, and you use them as the finished items. For instance, you can use cloth or wood to create things like furniture or shirts.
- Indirect material: is the material used in the production of completed goods but cannot be ascribed to particular physical units. Using a saw to cut wood for furniture or a pair of scissors to cut fabric for shirts are two examples.
Labour Cost
Labour refers to the people who can turn raw materials into finished things.
- Direct labour consists of people who participate actively in the production of goods. For instance, people working in manufacturing or production units refer to direct labour.
- Indirect labour refers to employees whose work you cannot specifically attribute to one product and who do not directly involve in the manufacturing process. For instance, salespeople and directors fall under indirect labour.
Expenses
Costs incurred by a firm usually fall into this category, except for material and labour costs.
- Direct expenses: are connected to particular cost units and are also known as chargeable expenses, like the cost of direct labour, raw material costs, utilities, and rent.
- Indirect expenses: any expense that does not qualify as direct is an indirect expense, such as printing expenses, utility expenditures, and legal advice.
Overhead Costs
Overhead charges are comparable to indirect costs. However, “overhead” has a broader definition that includes indirect labour, materials, and expenses. The following are the three categories that categorise overhead expenses:
- Factory overhead: refer to the costs associated with manufacturing, production, or other expenses necessary for the efficient operation of a factory. Utilities, insurance, and manufacturing rent are a few examples.
- Office and administrative overhead: refers to the cost associated with managing and running a business, such as an office equipment like printers and stationery.
- Selling and distribution overhead: means the costs associated with marketing a product, obtaining orders, and distributing goods and services.
Also read about:
Cost Accounting Methods
Cost accounting techniques are of four types:
- Standard cost accounting: uses ratios to assess how well you use labour and materials to manufacture things in a typical setting.
- Activity-based cost accounting: is a method that uses a specific good or service to assign the cost of each organisation’s operation. The activity analysis decides these cost categories, improving the cost accuracy of goods and services.
- Lean accounting: is a collection of principles and procedures that manufacturers use to receive quantitative feedback. Lean accounting emphasises visual and lean-focused performance measurements rather than activity-based or standard costing. The price of producing an extra output unit is called the marginal cost is a new name for this approach.
- Marginal cost: A marginal cost analysis can investigate the relationship between production volume, selling price, costs, expenses, and profits by subtracting the variable cost from the revenue and dividing the result by the revenue.
In conclusion of cost accounting, don’t forget to make it a point to equip yourself with cost accounting to know the cost of producing every single item for your company.
Read more articles related to Working Capital
Working Capital Management
Contra Entry
Types Of Working Capital